Ultrasonic Shear wave Inspection is a non-destructive testing technique that uses high-frequency sound waves to detect internal flaws and defects in materials such as metals, composites, and plastics.
Our team of highly experienced certified professionals offers quality industrial ultrasonic shear wave inspection in Grande Prairie and the Peace Region. We use the latest technology to ensure you get the information you need.
Our certified level 3 professional has 15 years of experience in the NDT industry and practises precision and attention to detail on every job. Through ongoing training, our team stays current on all the latest codes and industry requirements, ensuring a high inspection quality standard.
Call us today, and we can ensure that the components in your project meet industry standards and regulatory requirements.
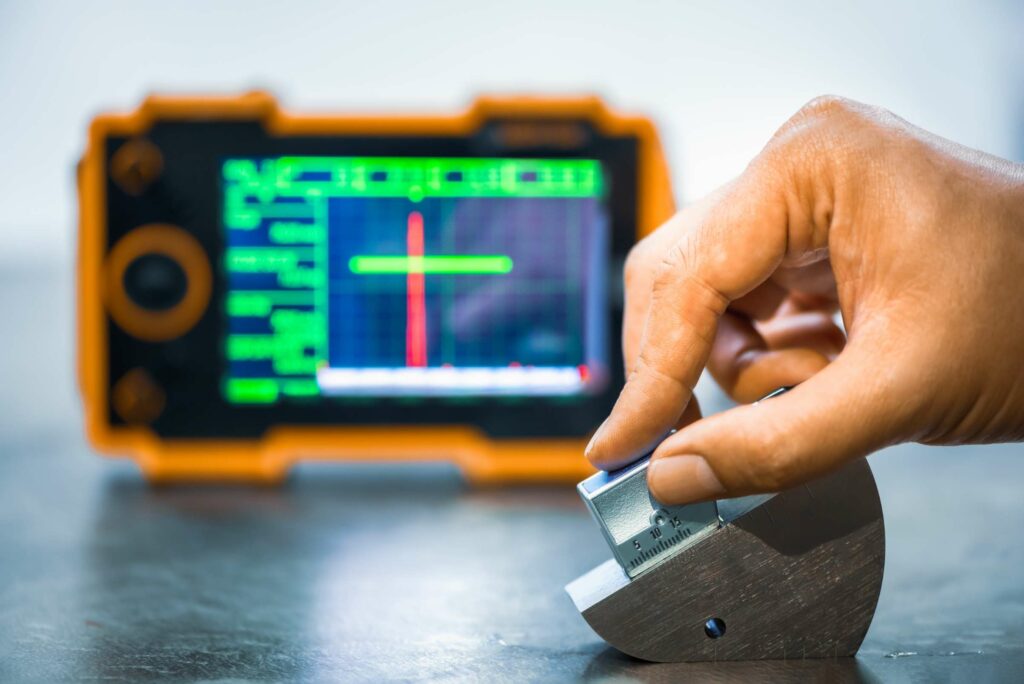
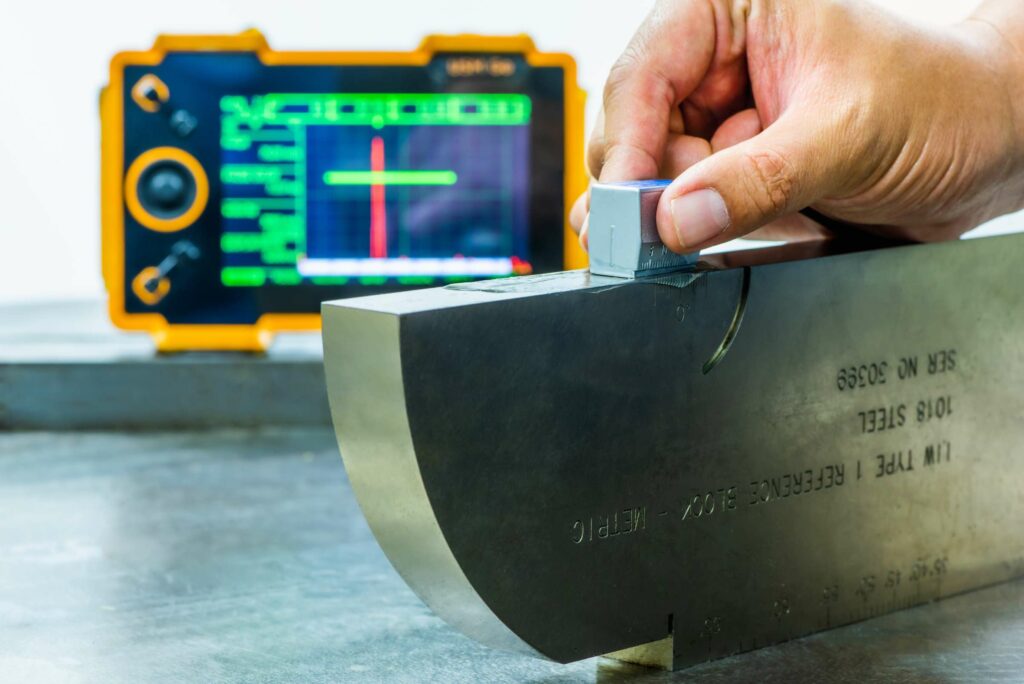
What is Ultrasonic Shear Wave Inspection?
Unlike ultrasonic thickness testing, which uses longitudinal waves that travel in the same direction as the beam, shear waves travel perpendicular to the beam. They can detect flaws that are difficult to identify with longitudinal waves alone. Shear waves are beneficial for detecting defects in welds by sending the beam in at an angle through the adjacent parent material.
During a shear wave inspection, an ultrasonic transducer is placed on the adjacent material’s surface and emits high-frequency sound waves into the inspection material. These waves reflect off the material’s internal surfaces and are picked up by the transducer. The data collected by the transducer is analyzed to identify any defects or irregularities in the material.
What are the Uses of Ultrasonic Shear Wave Inspection?
Ultrasonic Shear wave Inspection is a valuable non-destructive testing technique that has several uses in the oil and gas industry, including:
1. Weld Inspection:
Shear wave inspection can inspect welds for defects such as cracks, porosity, and lack of fusion. This is important in ensuring the structural integrity of pile splices, I-beam splices, pipelines, pressure vessels, and other components used in the oil and gas industry.
2. Flaw Detection:
Shearwave inspection can detect flaws in components such as valves, pumps, and turbines. This can help identify potential failure points and ensure these components operate at peak efficiency.
Overall, ultrasonic shearwave inspection is a critical tool in ensuring the safety and reliability of your next project.
What are the Benefits of Ultrasonic Shear Wave Inspection?
There are several benefits of using ultrasonic shearwave inspection, including:
1. Non-Destructive Testing:
Ultrasonic shearwave inspection is a non-destructive testing technique, which means it cannot damage or alter anything while inspecting materials and components. This is important when equipment and infrastructure are expensive and difficult to replace.
2. Accuracy:
Shear wave inspection is highly accurate and can detect flaws and defects that may not be visible to the naked eye. This can help identify potential failure points and prevent costly downtime and repairs.
3. Versatility:
Ultrasonic shear wave inspection can inspect a wide range of materials and components, including metals, composites, and plastics.
5. Safety:
Ultrasonic shear wave inspection is a safe testing method that does not expose workers to radiation or other hazards.
Overall, ultrasonic shear wave inspection is a valuable tool, helping to ensure the safety, reliability, and efficiency of equipment and infrastructure.