A non-destructive testing technique, magnetic particle inspection (MPI) detects surface and slightly subsurface flaws in ferromagnetic materials. Ferromagnetic materials include iron, cobalt, nickel, and their alloys. Materials commonly found in motors, generators, and transformers. MPI is a quick and effective method of detecting flaws.
Our team of highly experienced certified professionals offers quality industrial magnetic particle inspection in Grande Prairie and the Peace Region. Our team ensures you get the information you need.
Our certified magnetic particle inspection professional has 15 years of experience in the NDT industry and practises precision and attention to detail on every job. Through ongoing training, our team stays current on all the latest codes and industry requirements, ensuring a high inspection quality standard.
Call us today, and we can ensure that the components in your project meet industry standards and regulatory requirements.
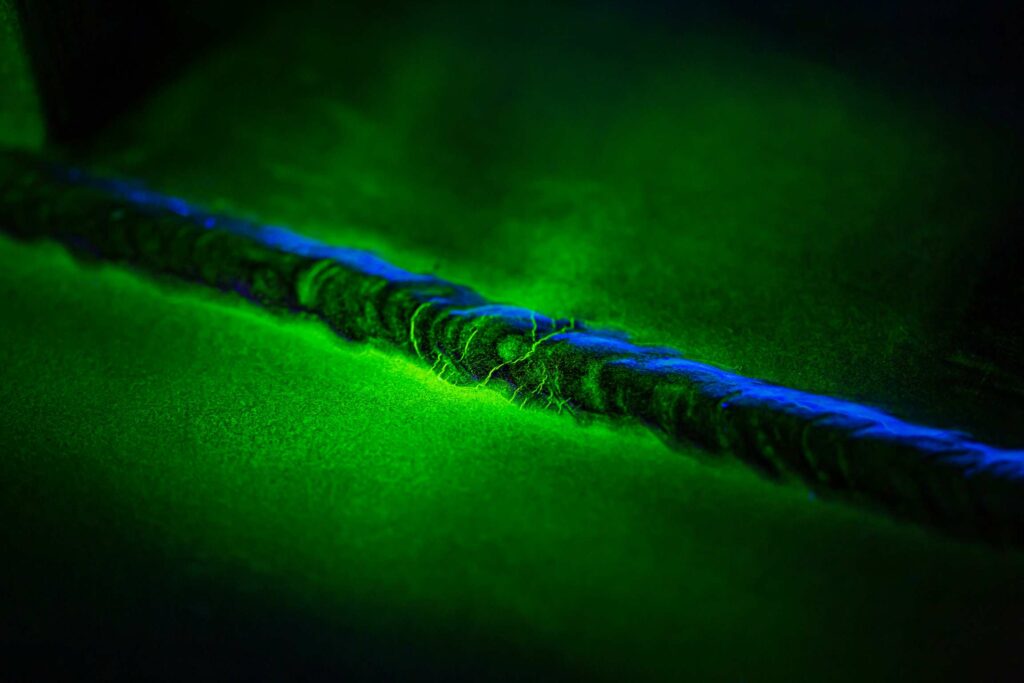
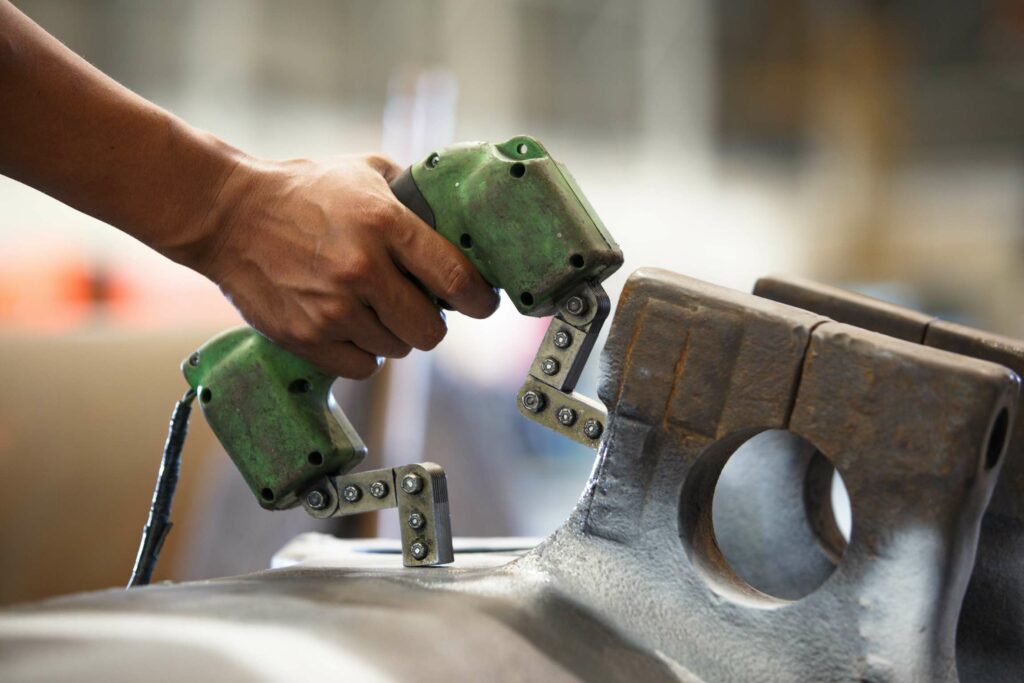
What is Magnetic Particle Inspection?
Magnetic particle inspection involves magnetizing the material under examination and applying iron oxide or other magnetic particles to the surface. Suppose there are any surface or subsurface flaws in the material. In that case, the magnetic flux will leak out of the material, causing the magnetic particles to be attracted to the flawed area. The particles will accumulate at the flaw’s location, forming an easily visible indication of the fault on the material’s surface.
What are the Uses of Magnetic Particle Inspection?
Magnetic Particle Inspection (MPI) can inspect critical equipment components such as pipelines, valves, drill pipes, and other metallic parts. Here are some of the specific uses of MPI:
1. Weld inspections:
MPI is used to inspect welds in pipes, tanks, and other equipment. It also inspects a pipeline’s welding to detect cracks, porosity, or defects that may cause leaks.
2. Surface inspections:
MPI can be used to inspect the surface of metallic parts for cracks, corrosion, and other defects that may occur due to fatigue or stress.
3. Non-destructive testing of equipment:
MPI can inspect equipment’s metallic components without damaging anything.
4. Quality control:
MPI ensures that the materials and components meet the required quality standards.
5. Maintenance and inspection of structures:
MPI can be used to inspect the metallic components of structures, such as drilling rigs, platforms, and pipelines, to detect defects that may cause failures and accidents.
Magnetic particle inspection is a valuable tool to ensure the safety and reliability of critical equipment and structures.
What are the Benefits of Magnetic Particle Inspection?
Magnetic Particle Inspection (MPI) offers several benefits over other non-destructive testing methods, as well as visual inspection, including:
1. Cost-effective:
MPI is a cost-effective method to detect surface and slightly subsurface flaws in any ferromagnetic material. It is much less expensive than other non-destructive testing methods, such as radiography and ultrasonic testing.
2. Non-destructive:
MPI is a non-destructive testing method that does not damage or alter the material under inspection. Leaving the material undamaged is particularly important when components are expensive and difficult to replace.
3. Quick and easy:
MPI is a relatively quick and easy method of inspecting components for surface and slightly subsurface defects. The results are easily visible and interpretable.
4. High sensitivity:
MPI is a highly sensitive method of detecting surface and slightly subsurface flaws in ferromagnetic materials. It can detect flaws as small as 0.001 mm in size, which may not be visible to the naked eye.
5. Versatility:
MPI is used on various ferromagnetic materials, including steel, iron, nickel, and cobalt alloys. It is also suitable for inspecting components of different shapes and sizes, from small parts to large structures.